The North American tire market is currently grappling with unforeseen shipping challenges that are disrupting supply chains. Geopolitical conflicts and piracy incidents near Yemen in the Red sea have led to rerouting of vessels, causing delays and escalating shipping surcharges. In this article, we’ll explore the impacts of these disruptions on inventory management, pricing dynamics, and strategies for navigating these challenges in the tire industry.
Table of Contents
I. Unforeseen Shipping Challenges
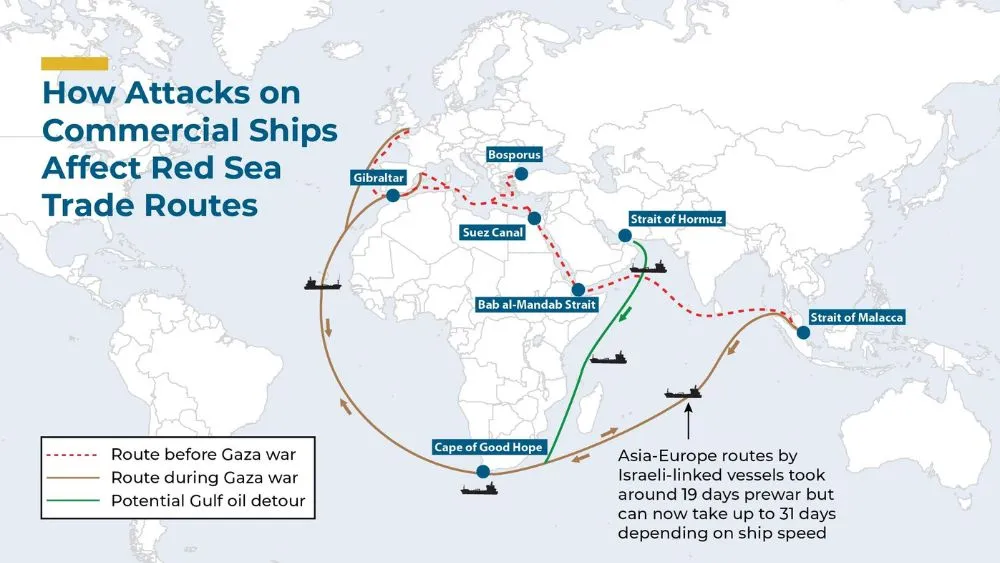
A. Introduction to disruptions impacting the North American tire market
Iran backed Houthi attacks off the coast of Yemen in the Red Sea have set off a chain reaction affecting shippers bound for Europe and the U.S East Coast, forcing them to seek alternate routes around Africa. While the conflict in the Middle East may seem distant, its repercussions are keenly felt in the North American tire industry, causing significant disruptions in inventory management and pricing dynamics.
B. Impacts of geopolitical conflicts and piracy incidents near Yemen
Due to attacks on ships by Iranian-backed Houthis in Bab al Mandab Strait, global shipping routes through the Suez Canal are being changed. Many shipping companies are now choosing longer routes around Africa instead. This change is affecting trade between Asia and Europe and causing a shortage of ships, which is making ocean freight prices go up.
C. Rerouting of global shipping routes and resulting complications
With approximately 90% of container ships that would typically cross the Red Sea now redirected around the Cape of Good Hope, logistics have been severely impacted. Companies have resorted to altering their shipping routes, adding congestion to existing paths from eastern Asian ports to the U.S. West Coast. Moreover, reduced shipping capacity via the Panama Canal, compounded by low water levels due to regional droughts, has further compounded the shipping woes, causing delays, container shortages, and escalating shipping surcharges.
II. Turbulence in Transit
A. Lengthening of transit times and rerouting of vessels around Africa
The longer voyage around Africa has significantly extended transit times, exacerbating delays and complicating logistics for tire shipments to North America. Moreover, rerouting vessels through alternative passages has added strain to established shipping routes, further disrupting the flow of goods.
B. Congestion and strain on shipping routes from China to the U.S. West Coast
The shift from Atlantic to Pacific routes for some companies has led to congestion on paths from eastern Asian ports to the U.S. West Coast, intensifying competition for limited shipping capacity and exacerbating delays in tire deliveries. It’s like rush hour traffic on the high seas!
C. Bottlenecks at the Panama Canal due to water level issues
Amidst the shipping challenges the Panama Canal is encountering a low water levels problem due to regional droughts. This issue is leading to slowdowns in shipping traffic which results in shipments bound for East Coast ports are experiencing further delays.
D. Delays, container shortages, and escalation of shipping surcharges
The disruptions have caused delays in shipments and made it challenging to secure empty cargo containers. Additionally, there has been a sharp increase in shipping surcharges since late December. The fluctuating surcharges have introduced unpredictability to shipping costs, creating additional challenges for tire makers and importers.
“In theory, the impact on North American supply chains should be fundamentally smaller than that on Europe given the availability of trans-Pacific routings to the U.S. west coast,” said S&P Global, which provides data and intelligence analysis. “Yet, the Americas have also more directly suffered the effects of reduced shipping capacity via the Panama Canal. Shipping via the Suez Canal was a secondary option for liners looking to reduce their exposure to the Panama Canal.”
III. Inventory Management Hurdles
A. Proactive responses from tire manufacturers and importers to mitigate disruptions
Tire manufacturers and importers have taken proactive measures to address disruptions in raw materials deliveries and tire shipments to customers. Companies like Pirelli, Continental, Group Michelin, and BKT USA Inc. have implemented various strategies to ensure the continuity of their operations amidst the shipping challenges.
B. Disruption to production and delivery schedules, affecting inventory levels
Due to shipping disruptions, there are production delays and longer delivery times, affecting tire inventory levels. This shortage is particularly noticeable for OTR tires and those necessary for the upcoming planting season.
C. Challenges in maintaining sufficient inventory, particularly for OTR tires
St. Louis Wholesale Tire and other distributors are finding it challenging to keep up with the demand for OTR tires, particularly during the busy planting season. To manage this, they’re implementing proactive inventory strategies to ensure sufficient stock levels.
“It’s not as bad as the height of the COVID dilemma — thank goodness, right?” remarked Joseph Inchiostro, CEO of St. Louis Wholesale Tire.
Reflecting on recent challenges, he expressed, “It’s just a little frustrating because we just went through those years of the nightmare of our logistics chains through the whole COVID epidemic and ports being congested and vessels and shortages of containers.”
Inchiostro continued, “And we really went into this year thinking it would be back to good old-fashioned tire selling and competition. But here we go again with a little hiccup, and it really highlights how delicate international shipping lanes are and how dependent we are in the United States that they’re running smoothly. Just even the slightest hiccup, the ripple effect is staggering.”
D. Strategies employed by distributors to manage inventory and meet demand
Tire Group International (TGI) and similar distributors are rethinking their inventory management tactics to tackle the uncertainties and variations in shipping. Despite these logistical complexities, they remain dedicated to delivering products promptly to customers, employing adaptable strategies to overcome challenges.
IV. Pricing Pressures
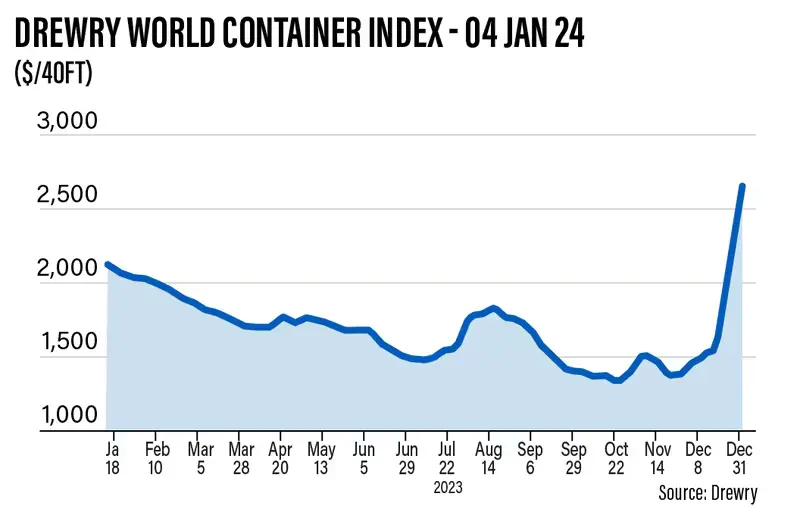
A. Surge in freight rates and fluctuations in shipping surcharges
The disruptions in global shipping have caused freight rates to skyrocket, with shipping surcharges surging by an average of 12% to 13% across all shipment points to the U.S. This steep increase in costs is squeezing tire importers and distributors, impacting their profit margins and pricing dynamics.
Global Rubber Industries (Pvt) Ltd. of Sri Lanka said rerouted vessels have resulted in longer lead times and higher costs. Due to high demand and time constraints, vessels opt to omit some ports, resulting in blank sailing and unpredictability of vessel schedules.
B. Balancing the pass-through of surcharges to customers and preserving margins
Importers like TGI and St. Louis Wholesale Tire are wrestling with the challenge of deciding whether to pass on the heightened surcharges to customers or absorb them to uphold competitive pricing and safeguard margins. The unpredictable fluctuations in shipping costs only compound the complexity of pricing decisions, introducing heightened uncertainty into the equation.
C. Initiatives such as additional freight surcharges to counter rising costs
To address the mounting shipping expenses, firms such as BKT USA Inc. have implemented additional freight surcharges on shipments. This adjustment mirrors the tripled ocean freight rates observed since November. The objective of these measures is to mitigate the impact of rising shipping costs on the company’s profitability.
V. Navigating Solutions
A. Customers’ resilience in continuing to order imported tires despite increased expenses
Despite the increasing costs and delays, customers exhibit resilience by persisting in ordering imported tires to fulfill their needs. Their willingness to accept the higher costs underscores the significance of maintaining sufficient inventory levels and ensuring punctual deliveries.
B. Adoption of proactive measures by importers to secure shipping containers and manage logistics
Importers are adopting proactive measures to address the shipping challenges, such as assigning carriers well in advance to secure empty containers and minimize delays. Transparent communication and proactive planning are key to navigating the complexities of international shipping in turbulent times.
C. The pivotal role of transparent communication in addressing challenges and setting expectations
Effective communication is essential for managing the hurdles presented by global shipping disruptions. Importers, distributors, and customers must maintain transparent channels, setting practical expectations and resolving issues promptly. This proactive strategy helps minimize disruptions to supply chains and strengthens relationships within the industry.
VI. Conclusion: Plotting Our Path Forward
A. Reflecting on Insights from Tire Experts and Industry Voices
The hurdles stemming from global shipping disruptions shed light on how tightly woven the tire industry is and underscore the need for joint problem-solving. Drawing on the wisdom of tire experts and industry voices, we glean valuable insights to steer through the current challenges and illuminate the road ahead.
B. Putting a Spotlight on Flexibility and Teamwork to Navigate Shipping Woes in North America’s Tire Market
To overcome the shipping disruptions affecting the North American tire market, adaptability and collaboration are essential. By embracing proactive measures, maintaining transparent communication, and forming collaborative partnerships, stakeholders can effectively mitigate the impact of shipping challenges and ensure the resilience of the tire industry amidst adversity.
Frequently Asked Questions
How are Iran-backed Houthi attacks impacting the North American tire industry?
The Iran-backed Houthi attacks near Yemen in the Bab al Mandab Strait have disrupted global shipping routes, causing delays and escalating shipping surcharges. This has led to significant challenges in inventory management and pricing dynamics for the North American tire market.
What are the main challenges faced by tire manufacturers and importers amidst these shipping disruptions?
Tire manufacturers and importers are grappling with production delays, longer delivery times, and difficulties in maintaining sufficient inventory levels, particularly for OTR tires. These challenges stem from rerouted shipping routes, increased transit times, and bottlenecks at key transit points like the Panama Canal.
How are distributors adapting to manage inventory and meet demand during these disruptions?
Distributors are implementing proactive inventory strategies to ensure sufficient stock levels despite the challenges. Rethinking inventory management tactics and maintaining adaptable strategies are crucial for overcoming uncertainties and variations in shipping.
What measures are importers taking to address shipping challenges and secure shipments?
Importers are adopting proactive measures such as assigning carriers well in advance to secure empty containers and minimize delays. Transparent communication and proactive planning are key to navigating the complexities of international shipping during turbulent times.
How can stakeholders in the tire industry navigate these shipping disruptions effectively?
Stakeholders can navigate shipping disruptions by embracing adaptability and collaboration. By taking proactive measures, maintaining transparent communication, and forming collaborative partnerships, they can effectively mitigate the impact of shipping challenges and ensure the resilience of the tire industry amidst adversity.